Industry 5.0 : 스마트 팩토리 주요 기술 동향
●
●
●
* 본 내용은 김준호 매니저(☎ 02-6400-4714, kerouac1@naver.com)에게 문의하시기 바랍니다.
** 본 내용은 필자의 주관적인 의견이며 IITP의 공식적인 입장이 아님을 밝힙니다.
팬데믹이 한창이던 2020년 유럽연합(EU)은 Industry 5.0을 발표하였다. Industry 4.0이 스마트팩토리를 디지털 기술과 공장 자동화라는 기술적 관점에서 언급하였다면, Industry 5.0은 기술적 관점에서 더 나아가 인간과 기술의 협업을 강조하며 로봇, 디지털트윈 등의 기술을 강조하였다. 스마트팩토리는 2016년 다보스포럼(Davos Forum)에서 세계경제포럼을 창시한 클라우스 슈밥(Klaus Schwab)의 Industry 4.0에서 본격적으로 언급되었으며, 제조업의 새로운 패러다임의 시작을 알린 바 있다. 이후 펜데믹으로 인한 글로벌 공급망 문제, 탈세계화에 따른 선진국의 온쇼어링이 확산됨에 따라 스마트팩토리는 더욱 빠르게 전세계에 퍼져 나갔다. 특히, 우리나라의 경우 인구 고령화와 생산인구 감소로 인해 스마트팩토리가 다시 주목받고 있으며, 기존 공장에 적용뿐 아니라, 신규 공장 신설 시 적극적으로 도입되고 있다. 이에 다시 산업기술로 떠오르고 있는 스마트팩토리의 주요 기술과 적용 사례를 살펴보고 향후 기술발전 방향을 전망해 보고자한다.
II. 스마트팩토리 주요기술
1. 스마트팩토리 정의 스마트팩토리란 정보통신기술을 활용하여 제품의 설계, 개발 및 생산 과정에서의 데이터와 완성품 및 부품, 원자재 등에 대한 데이터를 수집한 뒤 이를 디지털화하고 모든 공정에서 데이터를 공유, 교환하며 유기적으로 연결하는 공장을 의미한다[1]. 지능형 공장이라고도 일컬어지며 2004년 독일의 엔지니어이자 교수인 데플레프 쥘케(Detlet Zuhlke)는 ‘모든 공정, 생산품, 생산요소를 디지털화 하고 서로 네트워킹하는 공장’으로 정의하기도 하였다.
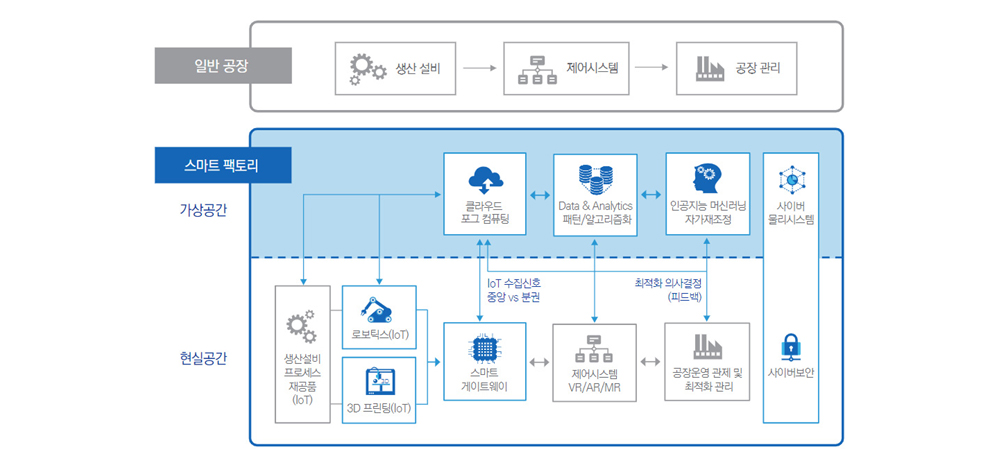
<자료>삼정KPMG, 4차 산업혁명과 제조혁신, 2018.
[그림 1] 스마트팩토리 기술구조
스마트팩토리는 공장 내 설비와 기계에 센서(IoT, Internet of Things)를 설치하여 데이터를 실시간으로 수집, 분석하며 공장 내 모든 상황들을 분석하여 목적에 맞게 스스로 자율적 제어가 가능한 공장을 의미한다. 클라우드, AI, AR/VR 기술이 종합적으로 적용되며, 스마트팩토리를 통해 제품기획에서부터 설계, 생산, 유통, 서비스 등 제품수명 주기 전 과정을 ICT 기술로 통합하여 최적화된 생산 시스템으로 구현된다[그림 1].
2. 공장 자동화와의 차이점 스마트팩토리 기술과 기존 공장 자동화(factory automation)의 가장 큰 차이점은 양방향 통신을 기반으로 작업 명령과 피드백이 가능하고, 스스로 생각하고 판단하는 공정이 적용된다는 점이다[2]. 즉, 컨베이어 시스템 기반의 연속 일관된 공정이 아닌 인공지능이 탑재된 각 설비와 기기가 스스로 판단하여 최적화된 다음 공정 모듈을 찾아 제품을 이동시키며 생산이 진행되는 구조로 이루어졌다는 것이다[3]. 생산 공정과 관련된 모든 기술과 디바이스가 서로 긴밀하게 네트워크를 형성하며, 공정을 스스로 판단하여 진행한다[표 1].
[표 1] 자동화 공장과 스마트팩토리 차이점
구분 | 자동화 공장 | 스마트팩토리 | 비고 |
---|---|---|---|
공정 단위 | 연속적(컨베이어벨트) | 모듈별 진행 | 수평적/수직적 공정 네트워크 도입 |
공정 진행 | 정해진 Sequence | 대기시간, 선ㆍ후 공정을 고려한 최적모듈로이동ㆍ진행 |
모듈과 카트 간의 정보 교환 |
부분품 이동 | 수동적 정해진 Route에서 Go/Stop |
능동적 최적공정모듈을 찾아 이동 |
스마트 카트로 이동 |
유지·보수 | 엔지니어가 진단, 조치 전체 공정라인 Stop |
자체 진단/원격 제어 문제발생모듈만 Stop |
문제 발생 전 예비 경보 중앙관제센터에서 조치 |
생산품목 | 획일적인 디자인과 규격 | Customized Product | 공정 진행 직전에도 디자인, 규격 등 변경 가능 |
<자료> 하나금융경영연구소, 스마트팩토리: 4차 산업혁명의 아이콘, 2018. 10. 4.
기존의 공장 자동화는 컨베이어 시스템을 기반으로 입력된 명령과 정해진 순서에 따라 반복되는 구조로 설계되었다면, 스마트팩토리는 인공지능 기술을 기반으로 제품 또는 반제품이 스스로 진행 상황을 파악해 최적화된 공정 모듈을 찾아 프로세싱하고, 생산이 진행되는 구조로 동일 기능의 복수 모듈이 작동하여 실시간으로 정보를 교환하며 공정 대기시간을 최소화 한다. 또한, 공정의 전후 프로세스 간 데이터를 자유롭게 연계하여 공정의 총체적 관점에서 최적화가 가능하여 대량 생산에 최적화된 공장 자동화와는 달리 다품종 소량 생산과 시장 수요에 신속 대응이 가능한 생산 유연성을 확보할 수 있다는 점에서 기존 공장 자동화와의 기술적 차이점이 있다.
3. 스마트팩토리 기술발전 방향 1970년대 이후 IT(Information Technoloty)와 OT(Operation Technology)의 기술 발전으로 공장 내 데이터를 연결, 수집, 분석하는 스마트팩토리 기술은 계속 진화 발전하고 있다. 스마트제조혁신추진단은 스마트팩토리의 기술 발전 수준을 5단계로 구분하고 있다[표 2].
[표 2] 스마트 공장 수준별 5단계 정의
구분 | 수준 정의 | 표준 | IoT 대상 | 특성 | 조건(구축 수준) | 주요 도구 |
---|---|---|---|---|---|---|
고도화 | 레벨 5 | 자율운영 | 작업자, 설비, 자재, 운전조건+환경 |
맞춤 및 자율 (맞춤형) |
모니터링부터 제어, 최적화까지 자율로 진행 |
인공지능, AR/VR,CPS등 |
중간2 | 레벨 4 | 최적화 | 작업자, 설비, 자재, 운전조건 |
최적화 (최적화됨) |
공정운영 시뮬레이션을 통해 사전대응 가능 |
센서 제어기 최적화도구 |
중간1 | 레벨 3 | 제어 | 작업자, 설비, 자재 | 분석 (분석) |
수집된 정보를 분석하여 제어 가능 |
센서+분석도구 |
기초 | 레벨 2 | 모니터링 | 작업자, 설비, 자재 | 측정 (측정됨) |
생산 정보의 모니터링이 실시간 가능함 |
센서 |
레벨 1 | 점검 | 자재 | 식별 (확인됨) |
부분적 표준화 및 데이터 관리 |
바코드 RFID |
<자료> 스마트제조혁신추진단 홈페이지
레벨 1~2단계는 기초적인 기술 수준으로, 공장 내 생산 정보가 디지털화된 단계이다. 바코드, RFID 등을 통해 생산 정보를 수집하고, 제품생산단위(Lot Number: LOT)별로 생산과정을 실시간으로 모니터링할 수 있다.
레벨 3단계는 생산설비, 공정, 자재 및 제품정보가 실시간 수집 분석하고 제어할 수 있는 단계를 의미하며, 생산 정보를 통해 품질분석이 가능하며 분석된 정보를 기반으로 생산계획을 세울 수 있다. 기업은 분석된 정보를 기반으로 생산 관련 주요 의사결정이 가능하다.
레벨 4단계는 시스템을 통한 생산 공정 제어와 사전 대응이 가능한 단계로, 수집 분석된 생산 정보를 기준으로 원인과 해결을 시스템이 스스로 판단 및 제어하여 생산이 최적화되는 단계이다. 이 단계에서는 분야별 관리시스템이 상호 실시간 연동될 뿐만 아니라 협력업체에게까지도 유기적인 정보 공유가 가능하다. 현재 대다수의 스마트팩토리의 기술 단계는 레벨 4 수준이다.
레벨 5단계는 IoT(Internet Of Things, 사물인터넷), CPS(Cyber Physical System, 가상물리시스템)를 기반으로 한 완성된 지능형 공장 수준이다. 모든 공정이 최적화되어 자율적으로 운영되며, 고객 요구에 즉시 생산, 배송되는 맞춤형 제조가 가능한 단계이다. 현재 스마트팩토리는 레벨 5단계의 자율생산체계를 목표로 기준 정보 기반의 설비, 도면, 매뉴얼, 자재 등의 정보를 디지털화하고, IoT 기반의 데이터를 연결하여 스마트화되어 가고 있다. 특히, 항공, 선박 등 중공업 산업에서는 디지털트윈 기술을 통한 내구도, 안전점점, 잔존수명 예측과 같은 분야로 그 적용 분야가 계속 확대되고 있으며, 곧 레벨 5단계의 스마트팩토리도 출현할 것으로 전망되고 있다.
4. 스마트팩토리 핵심기술 현재 스마트팩토리 구현을 위한 가장 핵심적인 기술로는 디지털트윈(Digital Twin), 인공지능, IoT, OT 보안기술을 꼽을 수 있다.
가. 디지털 트윈 디지털트윈은 도시, 제품, 공장, 인체 등 현실에서 존재하는 사물과 동일한 가상의 공간을 만들어 발생이 가능한 다양한 상황을 시뮬레이션하여 결과를 예측하는 기술이다. 신기술 개발이나 공장 내 새로운 설비를 도입하기 전 사용하여 투입 비용 및 시간을 절감할 수 있으며, 발생할 수 있는 위험을 사전 탐지함으로서 시뮬레이션에 기반 한 자율화된 공장 구현을 가능하게 한다[그림 2].

<자료> 정보통신전략위원회, 디지털 트윈 활성화 전략, 2021. 9.
[그림 2] 디지털트윈 요소기술 개념도
나. 인공지능(AI)
스마트팩토리는 공장에서 발생하는 데이터를 빅데이터 기술을 통해 수집, 분석하며 인공지능을 통해 최적화된 시스템을 구현한다. 대표적인 요소 기술은 다음과 같다.
① 머신 비전 기술(Machine Vision): 카메라를 이용하여 제조 과정에서의 결함 추적, 표면 마무리 검사, 부품들의 결함 검사 등에 사용되며, 공장 작업자들의 검사 작업을 대체하고 불량 검출율을 향상시키는 기술
② 지능형 설비 기술(Intelligence Manufacturing Detection): 생산 현장에서 발생하는 상황 대처를 자동화하는 기술로, 공정 목적을 자율적으로 인지, 판단, 제어하는 협업 제조 기술
③ 이상탐지 기술(Anomaly Detection): 제품생산 과정에서 이상 작동과 이상 상황이 발생할 때 불량이나 품질이 저하 요인을 자동으로 탐지하는 기술
④ 지능형 실감 인터렉션 가이드 기술(Real Sense Interaction Guide): 작업자의 작업 숙련도 향상을 위해 증강현실(Augmented Reality: AR), 가상현실(Virtual Reality: VR), 확장현실(eXtended Reality: XR) 기술을 도입하여 학습시간을 단축시켜 주거나, 제품 수율 향상에 도움을 주는 기술
⑤ 스마트 작업대 기술(Smart Workbench): 안전한 작업환경과 작업자 역할에 맞는 맞춤형 작업을 할당하여 생산성 향상 및 노동 피로도를 감소 시켜주는 기술
⑥ 제너레이티브 디자인 기술(Generative Design): 고객 요구에 적합한 제품을 생성형 AI를 이용하여 자동으로 생성 및 추천하며, 제품설계 전체 프로세스에 적용하여 설계비용을 절감하는 기술
다. IoT 공장에서의 IoT(Internet of Things, 사물 인터넷) 기술은 설비와 작업자 간, 설비와 설비 간 통신기술로 사용되며, 데이터 수집, 데이터 교환, 데이터 분석의 가장 근간이 되는 기술이다. 공장에서 사용되는 IoT는 산업용 IoT로 데이터 응답속도가 일반 소비자 IoT보다 상대적으로 빠르며 안정적이어야 한다. 최근에는 공장 내부에서 뿐만이 아니라 공장과 공장 간의 데이터 공유 및 분석에도 사용되고 있다. IoT 환경은 크게 생성(센서), 전달(네트워크), 통합 분석 및 제어(플랫폼) 기술로 나뉜다.
(1) IoT 센서 사물인터넷에서 사물을 담당하는 물리적인 측정 기기로, 생산환경의 변화, 제품 및 재고 현황, 생산과 관련된 상태 센서를 통해 감지하며, 측정된 데이터를 중앙의 서버나 컴퓨터로 전송한다. 최근에는 엣지 컴퓨팅 기술을 적용하여 센서 단계에서 분석과 제어 등의 기능을 직접 수행하기도 한다.
(2) IoT 네트워크 각 센서를 유무선 통신 기술을 통해 연결하는 인프라로, 각 센서에서 수집된 데이터를 플랫폼으로 전송하는 역할을 한다. 최근에는 5G 기술을 적용하여 초저지연, 초고속, 초연결, 초저전력의 특징을 나타낸다.
(3) IoT 플랫폼 수집된 데이터를 통합-분석-처리-시각화하며 다양한 공장 내 서비스 애플리케이션과 연동하고, 디바이스와 작업자를 유기적으로 연결하는 역할을 한다.
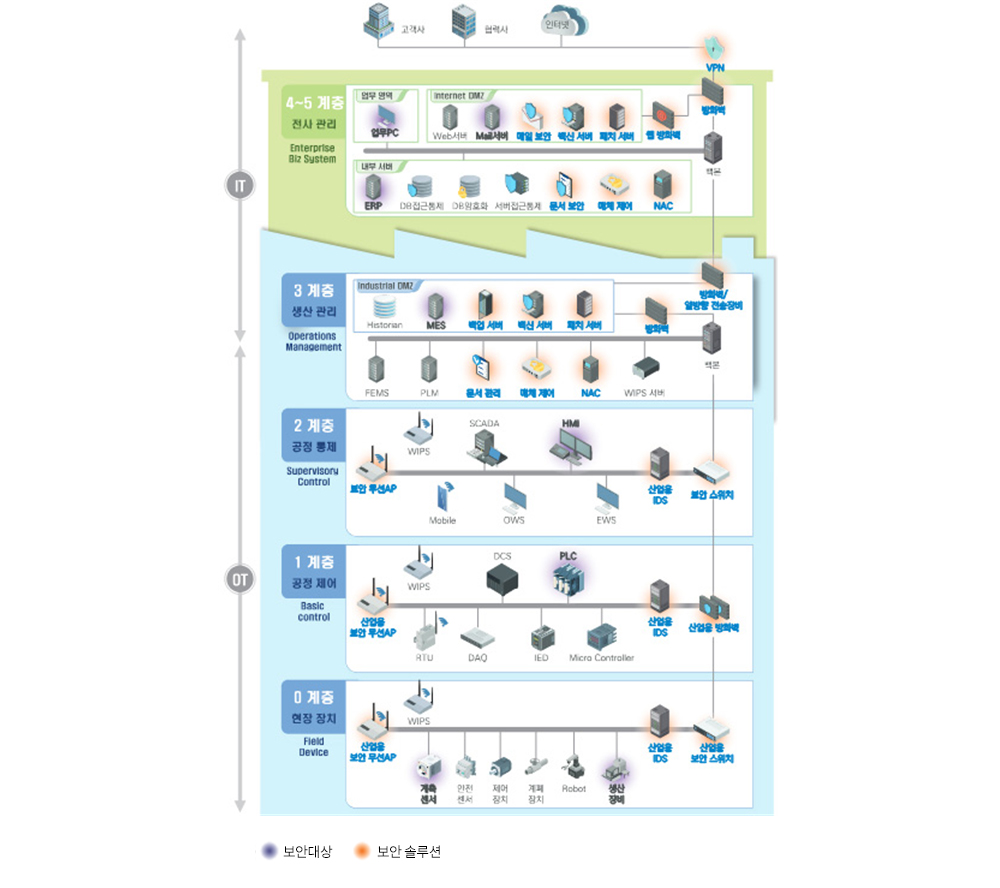
<자료> 한국인터넷진흥원(KISA), 스마트 공장 보안모델, 2020. 12.
[그림 3] 스마트팩토리 보안 아키텍처
(4) OT 보안
스마트팩토리 도입이 확대되면서, IT 영역 보안을 넘어 OT 보안(Operation Technology Security)에 대한 중요성이 부각되고 있다. 랜섬웨어의 경우 제조 공장에 대한 공격이 크게 증가하고 있다.
스마트팩토리의 보안 아키텍처는 총 5단계로 구분해 볼 수 있으며, OT 보안은 각 계층의 솔루션과 애플리케이션에 적용되어 데이터의 유출 및 불법적인 침입을 방지하는 기능을 한다. 스마트팩토리의 보안 아키텍처는 현장장치, 공정제어, 공정통제, 생산관리, 전사관리의 구조로 구분하여 볼 수 있다[그림 3].
5. Industry 5.0 유망기술 : 로봇 Industry 5.0에서는 인간과 로봇이 협업하는 코봇(Cobot)을 Industry 4.0과의 차이점으로 강조한다[4]. 현재 제조 현장에서도 지속적인 노동인구 감소와 자본투입 비용 증가로 인해 로봇 도입이 본격적으로 진행되고 있다. 이전의 공장 로봇이 높은 설비투자가 필요한 산업용 로봇에 한정되어 있었다면, AI, Mobile, 자율주행, 다관절 기술 발달로 사전 프로그래밍된 고정형 로봇에서 자유자재로 움직이며 능동적으로 협업하고 스스로 생각하여 자율적으로 작업하는 휴머노이드형 로봇으로 진화해 가고 있다. 이러한 휴머노이드형 로봇의 발전은 궁극적으로 제조업에서의 인간 노동을 대체하게 될 것으로 예측되고 있으며, 공장의 설비 자동화를 넘어 ‘인간 자동화’ 단계로까지 확대될 것으로 전망된다.
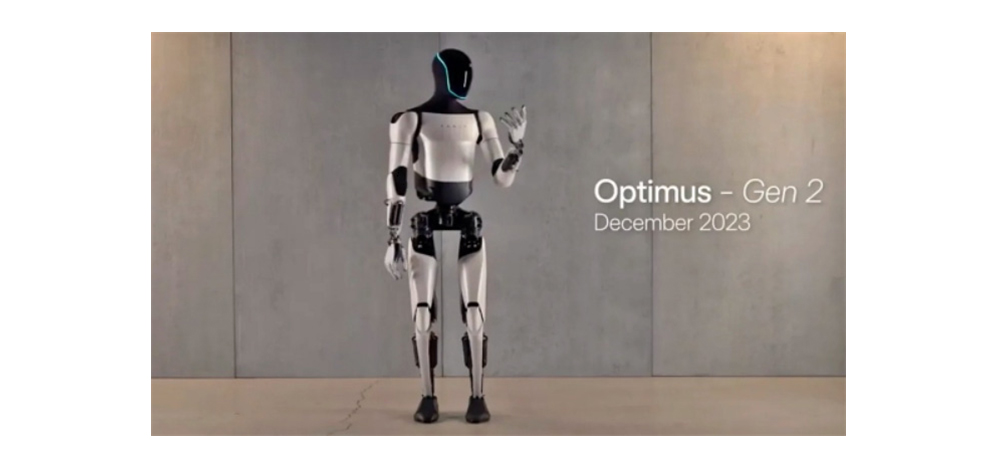
<자료> 테슬라 공식 유튜브 채널, Optimus Gen-2, https://youtu.be/cpraXaw7dyc?feature=shared
[그림 4] 옵티머스 Gen-2 홍보사진
스마트 공장에 도입될 수 있는 대표적인 로봇으로는 테슬라의 ‘옵티머스 젠2(Optimus Gen 2)’와 구글 딥마인드-스탠포드 대학이 협력 개발한 ‘모바일 알로하(Mobile ALOHA)’를 들 수 있다.
옵티머스 젠2는 2023년 12월 공개된 테슬라의 차세대 휴머노이드 로봇이다[그림 4]. 테슬라는 완전 자동화를 시도한 캘리포니아의 프리몬트 공장의 실패 이후 휴머노이드 개발에 심혈을 기울여 왔다. 옵티머스 젠2는 혹평을 받았던 전 작 모델과는 달리 테슬라가 자체 개발한 엑추에이터와 선서를 적용하여 보행 방식을 민첩하게 개선하였으며, 인공지능을 기반으로 주변환경 탐지 및 기억력이 획기적으로 개선되었다. 테슬라는 옵티머스 젠2를 공장 현장에 배치하여 자체 제조공정 과정에 활용할 예정이며, 성능이 검증되면 외부에 판매할 계획도 갖고 있다. 또한 테슬라는 옵티머스 젠2에 적용된 기술을 기반으로 테슬라 차량의 완전자율주행 및 딥러닝 기술도 고도화해 나갈 계획이다.
테슬라의 옵티머스 젠2와는 달리 가사 도움용 로봇으로 개발된 모바일 알로하는 이미테이션 알고리즘을 적용하여 인간을 관찰하여 데이터를 수집/학습하고 이를 기반으로 사람 없이도 가사를 수행하는 로봇이다. 인간의 행동을 모방하고, 지도학습 등을 통해 작업 수행 능력을 스스로 향상시키며 복잡한 작업도 90% 이상의 정확도로 수행할 수 있다. 구글은 모바일 알로하가 사람 대신 설거지를 하고, 옷을 개고, 요리도 하는 영상을 공개한 바 있다[그림 5]. 현재는 가사에 특화된 기능을 보이고 있으나, 곧 식당 등 소상공인을 대상으로 한 모델도 나올 것으로 예상되며, 제조 공장에 투입할 수 있는 공장형 로봇으로 진화될 것으로 전망된다. 무엇보다 모바일 알로하는 로봇의 상업화의 가장 큰 장애요소인 가격을 획기적으로 혁신하였다는 점을 주목할만한 데, 모바일 알로하는 대당 가격이 3만 2,000달러 수준으로, 기존 원격조종 로봇 대비 10분의 1 가격을 실현했다는 점에서 로봇 상용화의 전환점이 될 것으로 기대되고 있다.
두 가지 사례 외에도, 위험도가 높은 3D 작업에 투입할 수 있는 KUKA의 ‘도장용 로봇’, 무거운 짐을 적재하고 이동시키는 ‘팔레타이징 로봇’ 등 다양한 공장형 로봇 개발이 활발히 진행되고 있다.
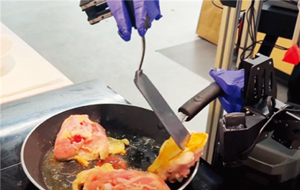
<자료> Stanford IRIS Lab 유튜브 채널, Mobile ALOHA Robot- Teleoperating a 3-Course Cantonese Meal)https://youtu.be/mnLVbwxSdNM?feature=shared
[그림 5] 모바일 알로하 시연(스탠포드 연구팀 동영상)
III. 스마트팩토리 주요 적용 사례
1. 국내 사례 대표적인 국내 스마트팩토리 사례로 삼성전자와 LG전자의 사례를 들 수 있다. 2023년 삼성전자는 온양, 천안공장에 세계 최초 반도체 패키징 무인화 라인을 가동했으며 무인화 비중은 20% 수준으로 알려져 있다[5]. 기존 반도체 전 공정에는 웨이퍼만 이동하는 방식이었고, 후 공정에서 기판, 트레이 등 여러 부품이 이동하는 방식으로 인력 투입율이 높았으나, 스마트팩토리 도입 후 웨이퍼 이송장치, 리프트, 컨베이어, 반송장비 등 설비 완전자동화를 실현하였다. 생산통합 모니터링으로 인력을 효율화하였으며. 설비 고장율은 90% 감소하였다. 삼성전자는 2030년까지 주요 글로벌 생산기지를 무인화할 계획을 갖고 있다고 발표하였다.
LG전자는 2022년 스마트파크 창원 공장을 설립했으며, 국내 가전업체 중 최초로 세계경제포럼(WEF)이 선정한 ‘등대공장’으로 선정되었다[그림 6]. 스마트팩토리의 핵심기술인 ‘디지털트윈’ 기술과 생산시설 전반에 AI, 빅데이터 등 디지털 기술을 적용하였다. 스마트파크에서는 수집된 대용량 데이터를 실시간 분석하여 제품의 불량률을 줄이고, 설비 고장을 사전 예방하는 시스템이 구현되었다. 디지털트윈 기술을 적용하여 실시간으로 생산과정을 시뮬레이션하며, 10분 뒤 생산 라인 상황을 예측할 수 있어 불량원인을 분석하는 시간을 50% 이상 단축하였으며, 불량률은 이전 대비 30% 감소한 것으로 발표하였다[6].
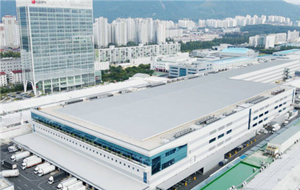
<자료> B!z Watch, “[르포] 묵은때 벗은 창원 LG스마트파크 ‘13초에 냉장고 한대 씩’”, 2022. 10. 10.
[그림 6] LG 스마트 파크
2. 해외 사례 최근 전 세계적으로 가장 주목 받는 스마트팩토리는 테슬라의 ‘Giga Factory(기가 팩토리)’이다. 테슬라는 2010년 GM/도요타 생산공장을 인수하여 자동화 공장으로 개조하였다. 생산성 증진을 위해 쿠카(KUKA), 화낙(FANUC)의 산업용 로봇을 도입하여 전체 생산과 조립, 검수까지 자동화 하였지만 완전 자동화 양산체계에는 실패하였다. 테슬라는 이러한 실패를 반면교사로, 보다 저렴하고, 더 거대한 규모의 생산이 가능한 기가 팩토리를 건설하였다. 새롭게 설립된 기가 팩토리에는 공정의 완전 자동화 및 최적화, 공장의 공간을 최적으로 설계하는 기술을 도입하여 성공적으로 오픈하였으며, 공장 규모 대비 생산성을 경쟁사인 도요타 대비 2배 이상 향상시키는 성과를 보였다. 기가 팩토리는 대부분의 공정을 로봇이 수행하며, 사람은 검수 업무 정도만 수행한다[표 3].
[표 3] 테슬라 공장의 스마트 공정
공정 과정 | 설명 |
---|---|
스마트 무브 | - 자동 이동 라인으로 로봇 카트가 공장 바닥에 깔리 자석 띠를 따라 제품을 이동 |
펜더 제작 | - 레이저 절단 로봇이 부품을 원하는 모양으로 자르면 프레스기를 통해 3차원 형상의 팬더로 제작 |
차체 제작 | - 독일제 쿠카 조립 로봇들이 알루미늄과 철제 부품들로 차체를 제작 - 고해상도 3D 카메라로 드릴, 용접, 리벳 가공 등을 정밀하게 수행 |
스탬핑 | - 스탬핑센터에서 알루미늄 원료를 후드, 범퍼, 패널 등으로 가공 |
최종 검수 | - 사람이 죄석, 도어 핸들 계기판 등을 부착하는 마무리 작업 |
<자료> 삼정KPMG, 4차 산업혁명과 제조혁신, 2018.
스마트팩토리를 이야기할 때 빼놓을 수 없는 기업 중 하나는 지멘스이다. 지멘스의 암베르크 공장은 설비자동화, 디지털트윈 및 센서를 통해 데이터를 수집 활용하고 있으며, 이러한 기술을 통해 제조현장의 상황을 실시간으로 모니터링하며 제어하고 있다.
지멘스는 디지털트윈을 통해 가상의 제품 생산을 사전에 시뮬레이션 해 봄으로서 제품 개발 및 생산 시간을 획기적으로 절감하고 있으며, 불량 문제 또한 크게 개선하고 있다.
3. 스마트팩토리 기술 공급기업
국외의 경우, 공장자동화 솔루션 및 IT기업이 스마트팩토리 기술 공급자로 포진하고 있다. 대표적인 공장자동화 솔루션 기업으로는 지멘스, 로크웰, 허니웰, ABB를 꼽을 수 있으며, IT기업으로는 SAP, ORACLE, CISCO 등을 들 수 있다[그림 7].
국내의 경우, IT 서비스 기업 중심으로 스마트팩토리 기술이 공급되고 있다. 대표적인 기업은 삼성SDS로 AI 기반의 인텔리전트팩토리 플랫폼을 표방하는 ‘넥스플랜트’(Nexplant)를 개발하여 공급하고 있다. 넥스플랜트는 인텔리전트 플랫폼으로 제조 전 영역을 지능화시켜 주는 플랫폼이며 설계/시공, 제조, 물류/Facility에 요구되는 기술을 플랫폼 기반으로 제공하고 있다.

<자료> 한국과학기술정보연구원, 스마트 팩토리 시장의 트랜드 변화와 시사점, 2021.
[그림 7] 스마트팩토리 기술 공급기업
LG CNS의 경우, 버츄얼 팩토리를 표방하며 ‘팩토바’(Factova)라는 스마트팩토리 플랫폼을 공급하고 있다. LG CNS는 버츄얼 팩토리를 스마트팩토리의 상위 버전이라고 정의하고 있으며, 데이터와 가상화 DX 기술을 그 차이점으로 설명하고 있다. LG CNS는 LG전자, LG화학 등 관계사의 공장에 팩토바를 적용하며 공급을 확대해 나가고 있다.
SK주식회사 C&C의 경우, 스마트팩토리의 상위 개념으로 “디지털 팩토리”를 표방하며 스마트팩토리 기술을 제공하고 있다. 기존의 스마트팩토리가 생산 프로세스의 실시간 모니터링과 최적화에 초점을 두었다면, 디지털 팩토리는 제품설계 및 생산단계에서 디지털 기술을 활용하여 생산과정을 개선하는 것을 의미한다[7]. SK주식회사 C&C는 디지털 팩토리 도입을 위한 컨설팅부터 플랫폼 공급까지 전 영역의 디지털 팩토리 서비스를 제공하고 있다.
제철소를 기반으로 스마트팩토리 사업을 추진하고 있는 포스코DX는 이음5G 사업자로 선정되며 현장의 통신 모듈과 기기 간 IoT 역량을 강화했다. 이음 5G를 운송 철도 및 차량 자율주행과 크레인 무인화, 산업용 로봇제어 등과 같은 대용량 통신과 실시간 응답속도를 요구하는 현장에 적용하여 스마트팩토리 기술을 고도화 하고 있다[8]. 이음 5G는 특정 지역 또는 건물에서만 사용할 수 있는 5세대(5G) 이동통신망으로, 이동통신 사업자가 아닌 일반기업이 5G 주파수를 받아 직접 맞춤형 네트워크를 구축하여 활용할 수 있는 기술이며 공용 5G 망을 사용하지 않아 상대적으로 보안에 유리한 기술이다.
Ⅳ. 결론
탈세계화가 가속화됨에 따라 전세계 공장의 온쇼어링 추세가 확산되고 있다. 세계경제가 저성장의 사이클에 진입하게 되어 높은 인건비 해결과 생산성 향상을 위한 스마트팩토리 도입은 더욱 빠르게 확산될 것으로 전망된다. 인구구조학적 관점에서 생산인구가 급감할 우리나라의 경우 스마트팩토리 도입은 필수적이다. Chat GPT를 필두로 한 AI의 비약적 기술 발전과 로봇 기술의 발전 또한 스마트팩토리의 확산을 증폭시킬 것이다.
식당에서 서빙로봇을 마주치는 것이 낯설지 않은 시대가 되었다. 공장에서도 로봇이 인간을 대체하는 스마트한 공장을 볼 날도 멀지 않을 것으로 예측된다.
[1] 네이버 지식백과 (두산백과), 스마트팩토리
[2] 삼정KPMG, 4차 산업혁명과 제조혁신, 2018.
[3] 하나산업정보, 산업융합시리즈3호-스마트팩토리: 4차 산업혁명의 아이콘, 2018. 10. 4.
[4] The Science Times, 인더스트리 4.0시대에서 5.0시대로, 2021.03.22
[5] 전자신문, 삼성전자 세계최초 반도체 패키징 무인화 라인 가동, 2023. 8. 30.
[6] 연합뉴스, ’등대공장‘ 창원 LG스마트파크 제조업의 미래를 비춘다, 2022. 10. 10.
[7] SK주식회사 C&C 홈페이지
[8] 메가경제, 포스코DX, 철강 분야에 ‘이음5G’ 첫 도입...디지털전환 확산, 2023. 9. 12.