4차 산업혁명과 측정표준의 디지털화
●
●
●
* 본 내용은 권재용 책임연구원(☎ 042-868-5774, jykwon@kriss.re.kr)에게 문의하시기 바랍니다.
** 본 내용은 필자의 주관적인 의견이며 IITP의 공식적인 입장이 아님을 밝힙니다.
4차 산업혁명(The 4th Industrial Revolution)은 정보통신기술(ICT)의 융합으로 이루어진 혁신으로 지능형 디지털 기술을 적극적으로 설계, 제조, 개선 및 유통 등의 전반적인 산업 프로세스에 통합 적용하였다. 지능형 디지털 기술은 IoT 네트워크, 인공지능 (Artificial Intelligence: AI), 빅데이터, 로보틱스 등의 기술을 포함하며 스마트 제조와 지능형 공장(smart factory)을 구현한다. 지능형 공장의 수많은 센서로부터 측정된 데이터는 수집과 분류를 통해 최적의 의사결정을 위한 판단자료로써 최대의 생산성과 효율성, 유연성을 창출하는 데 활용된다.
인류가 걸어온 산업의 역사를 살펴보면 기존의 제품 생산 방식과 작업 방식을 완전히 바꾸는 ‘혁명’과 같은 혁신을 통해 생산성과 효율성이 획기적으로 향상되었다는 것을 알 수 있다. 최초의 산업혁명은 18세기 후반 영국에서 발명된 증기기관의 출현으로 산업 적으로 동물과 인간의 노동에 대한 의존도를 낮추었고, 제조 및 공학의 새로운 시대를 열었다. 2차 산업혁명은 19세기를 거치며 석유, 가스와 전기의 사용이 시작되어 생산 기계의 구축 및 운영이 편리해짐으로써 조립 설비 및 대량 생산 공정이 가능해졌다. 다시 말해 이 시기에는 과학과 산업이 본격적으로 결합하며 생산성의 혁신이 일어났다. 3차 산업혁명은 20세기 중반 무렵부터 등장한 컴퓨터, 인공위성, 인터넷의 발명으로 촉진된 정보통신기술 기반의 산업혁명으로 이 시기에는 로봇 및 PLC(Programmable Logic Controller) 등을 이용한 공장 자동화가 본격적으로 시작되었고 산업 데이터를 관리하고 분석하기 위한 전산화된 비즈니스 시스템이 출현하였다.
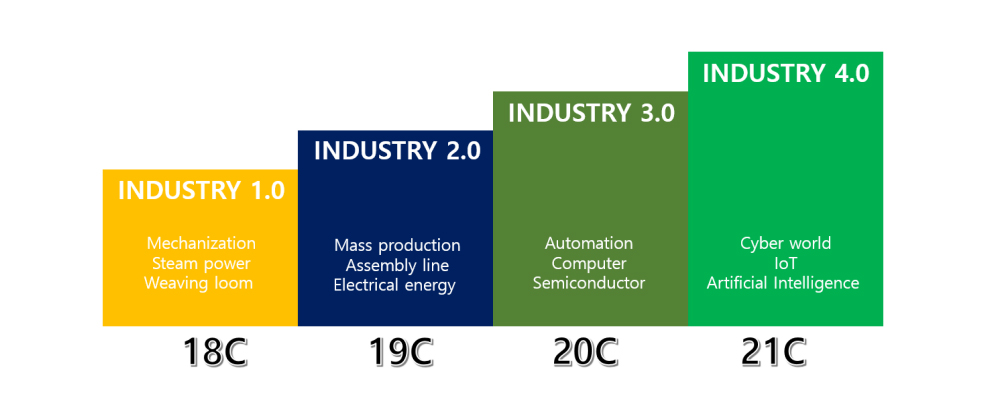
<자료> 한국표준과학연구원 자체 작성
[그림 1] 산업혁명의 단계별 특징
① 빅데이터 및 AI 분석: Industry 4.0 환경에서 빅데이터는 생산 현장의 장비, 설비 및 IoT 지원 기기뿐만 아니라 생산 현장 외부 세계의 다른 영역에서 생산되는 모든 데이터를 포괄적으로 의미한다. AI와 기계학습을 통해 빅데이터는 실시간으로 분석되어 제조 및 공급망 관리의 모든 영역에서 의사결정 및 자동화 개선에 활용 된다.
② 클라우드 컴퓨팅: 빅데이터를 엔지니어링, 공급망, 생산, 유통, 서비스 등 모든 가치 사슬 내에서 효율적으로 공유, 저장하여 유연하고 신속한 판단을 가능하게 한다.
③ 증강현실(Augmented Reality: AR): 일반적으로 디지털 콘텐츠를 실제 환경에 중첩하여 디지털화된 부품의 수리 또는 조립 지침을 원격지에 가상으로 전달하거나 사용자와 근로자를 위한 교육 콘텐츠의 시각화에 적용되어 몰입도가 높은 시스템의 유지보수, 서비스 관리, 품질 보증은 물론 근로자의 교육 및 안전 향상에 활용된다.
④ 산업용 사물인터넷(Industrial Internet of Things: IIoT): 장치, 로봇, 기계, 장비, 제품 등은 센서 및 RFID 태그를 사용하여 상태, 성능 또는 위치에 대한 실시간 데이터를 확보하며, 이 기술을 통해 기업은 원활한 공급망을 운영하고, 제품의 신속한 개선 설계, 설비 활용도 개선, 소비자 선호도 파악, 제품 추적 및 재고 관리를 한다.
⑤ 자율로봇: 인간의 노동력을 대체하는 제한적이고 단순 반복 작업뿐만 아니라 사람의 개입을 최소화하여 작업을 수행하도록 프로그래밍된 로봇이 활용된다. 자율로봇 역시 다양한 센서를 통해 주변의 정보를 모으고 AI 기반의 인식과 판단으로 다양한 임무를 수행한다.
⑥ 디지털트윈: IoT 센서 데이터를 기반으로 한 실제 기계, 제품, 프로세스 또는 시스템의 가상 시뮬레이션으로 현장의 생산 프로세스를 중단하지 않고 산업 시스템과 제품의 성능과 유지보수를 이해하고 분석 및 개선할 수 있다.
⑦ 사이버 보안: 가치사슬 내의 모든 사용자가 빅데이터에 접근할 수 있으므로 비인가 접근의 제어와 허용 레벨에 따른 데이터 접근 관리는 매우 중요하다. Zero Trust 아키텍처와 기계학습, 블록체인과 같은 기술을 적용하여 위협을 감지하고 예방할 수 있다.
산업기술의 고도화에 따라 현재까지 통용되고 있는 측정표준(measurement standard)의 전달체계는 대전환을 맞고 있다[3]. 지금까지는 [그림 2]와 같은 구도로 엄밀한 측정과학을 통한 측정표준이 개발되더라도 산업계의 활용은 다소 수동적인 방법인 인증서의 확보, 단순 교정 등으로 적용되어 산업현장에서의 실질적인 활용과는 거리가 있어 왔다. 4차 산업혁명의 핵심은 인간을 대신하여 환경을 측정하고 데이터를 수집하여 보고하며 필요에 따라 종단에서 자체적인 빠른 의사결정을 내리는 초연결과 초지능을 기본으로 한다. 이때 정확한 판단을 위해서는 측정표준을 기반으로 하는 다수의 다양하고 정확한 정보가 요구된다. 인간이 자율형 로봇이나 드론과 함께 일하는 복잡한 산업현장과 실생활 환경 에서 다양한 물리량을 측정할 수 있는 계측 센서를 이용하고 측정품질을 관리하는 일은 오작동, 안전사고 등의 잠재적인 위험 요소를 방지하고 관리하기 위해서 매우 중요하다. 센서, 계측장비에서부터 통신장비, 자동차에 이르기까지 향후 모든 산업 분야에 디지털 화된 측정표준을 기반으로 하는 정보체계와 관리가 도입될 것이다.
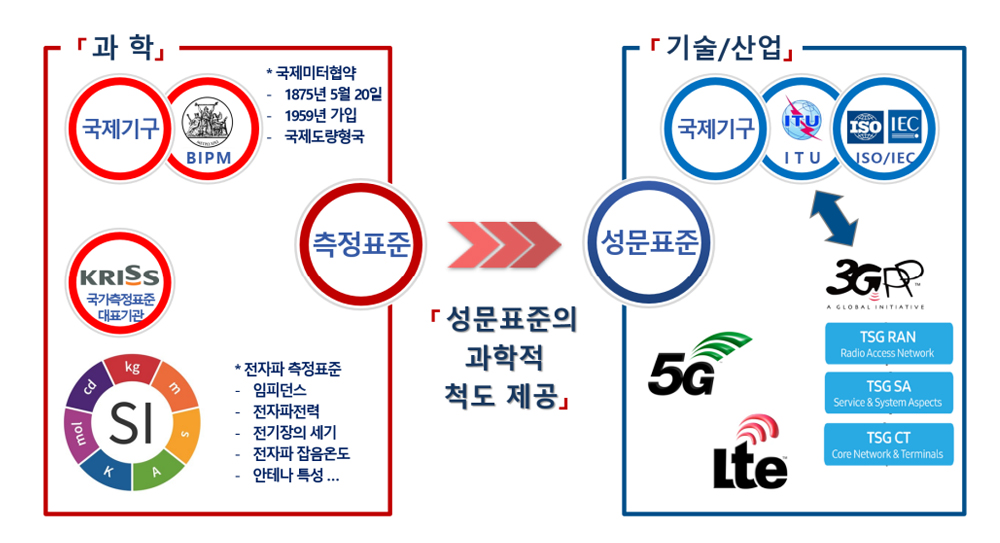
<자료> 한국표준과학연구원 자체 작성
[그림 2] 측정표준과 성문표준과의 관계(전자파 통신 분야 기준)
II. 측정표준의 디지털화
측정표준의 디지털화 동향을 살펴보면, 국제미터협약을 준수하고 이행하기 위한 전 세계의 국가측정표준기관(National Metrology Institute)들의 연합체인 국제도량형총회 (General Conference on Weights and Measures: CGPM)는 2022년부터 4차 산업 혁명 시대의 디지털 대전환에 대응하기 위해 디지털 프레임워크 기반의 데이터 공유방안 마련과 SI(International System of Units) 기본단위의 소급성 체계 디지털화를 위한 정책을 적극적으로 제안하고 추진하기로 하였으며 주요 국제기구(BIPM, OIML, IMEKO, ISC, CODATA, ISO, IEC, ILAC, CIE, NCSLI)1)도 SI 디지털 프레임워크의 개발, 구현 및 홍보를 지원하기로 공동 성명을 채택하였다. CIPM(International Committee for Weights and Measures) Digital SI Expert Group과 CODATA Working Group DRUM(Digital Representation of Units of Measurement)은 협업을 통해 “Call to action” 논문을 2022년 Nature지에 게재[4]하고 International Conference on DCC(Digital Calibration Certificates), SciDataCon, M4Dconf 등 국제학회를 개최 하여 국제적인 공감대 형성 및 지식 공유의 장을 마련하기 위해 노력하고 있다.
미국은 NIST(National Institute of Standards and Technology)를 중심으로 2021년 “디지털전환 워킹그룹”을 발족시키고, 2022년부터 5년간 연 2,500만 달러를 투입하는 ‘The Digital NIST’ 프로젝트를 승인하였다. XML 기반의 디지털 교정성적서 (Digital Calibration Certificate: DCC) 뿐만 아니라 디지털 표준물질인증서(Digital Reference Material Certificate: DRMC)를 발행하는 프로젝트를 통해 디지털 성적서와 인증서를 개발하고, 상호운용할 수 있는 측정 데이터, 계산, 법정계량 문서 등을 공유하는 클라우드 기반 시스템의 구축을 목표하고 있다[그림 3]. 이를 통해 인증, 적합성, 품질, 제품 안전 등에 대한 국제표준 요구사항을 충족시켜 미국 산업의 국제 경쟁력을 향상 시키는 것을 최종 목표로 한다.
1) BIPM: International Bureau of Weight and Measures, OIML: International Organization of Legal Metrology, IMEKO: International Measurement Confederation, ISC: International Science Council, CODATA: ISC’s Committee on Data, ISO: International Standardization Organization, IEC: International electrotechnical commission, ILAC: International laboratory accreditation cooperation, CIE: International commission on illumination, NCSLI: National Conference of Standards Laboratories, International
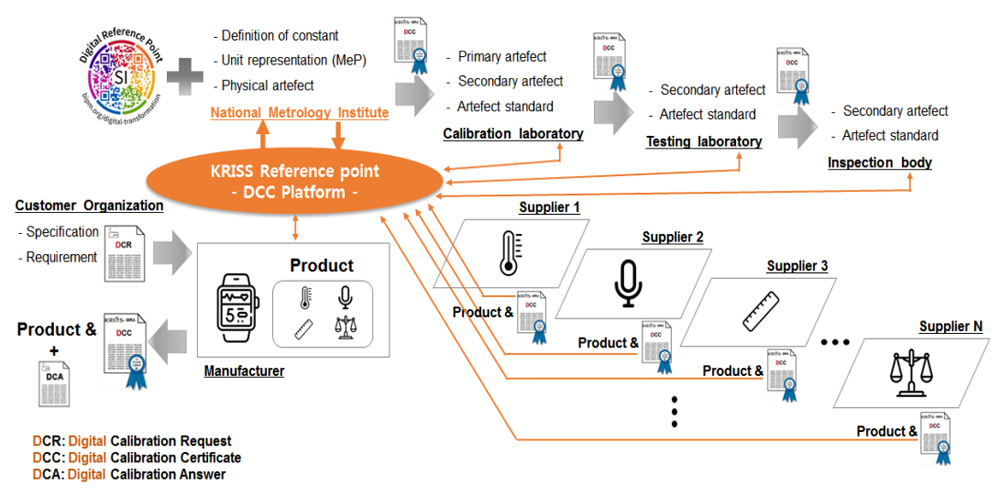
<자료> 한국표준과학연구원 자체 작성
[그림 3] 디지털 교정성적서(DCC) 매개 보급체계
독일은 PTB(Physikalisch-Technische Bundesanstalt)를 중심으로 독일연방 경제 에너지부로부터 1,200만 유로의 자금 지원을 받아 Bosch, Siemens, Zeiss, 프라운호퍼 연구소 및 여러 대학교와 함께 “디지털 전환을 위한 안전하고 견고하게 교정된 측정시스 템”을 목표로 협업 연구 중이다. 현실 영역뿐만 아니라 비 물리 센서 및 디지털트윈 영역 까지 포괄하여 ‘Truly digital workflows’의 구현과 그 과정에서 오가는 물리ㆍ가상 도메인 측정량의 신뢰성 보장 체계를 개발하고 있다. 이외에도 중국, 일본, 영국 등 우리 나라와 첨단 전략기술 확보에 각축하고 있는 주요 기술 선진국은 디지털 측정표준의 조기 확립 및 표준화 주도를 통한 기술 선점을 위해 노력하고 있다.
국내에서는 한국표준과학연구원을 중심으로 다음과 같은 국가측정표준 보급체계의 디지털화를 계획하고 있다[5].
① (고신뢰성 교정ㆍ시험 측정자동화기술) 디지털 교정성적서(DCC)에 담기는 핵심 측정 데이터 생산과정에서 휴먼에러를 최소화하기 위해 교정시험에 특화된 측정 자동화 로봇기술(H/W)(Automation Metrology), 교정시험 유형별 DUT(device under test)에 특화된 AI 판독기술 기반 측정 프로토콜 효율화 기술(S/W)(AI metrology), DCC 자동 생성 오류 최소화를 위한 측정 데이터 자동처리기술(Data metrology) 개발
② (아날로그 방식 국가측정표준 보급체계 디지털화) 측정 데이터와 DCC 자동생성 시스템 간의 표준화된 연결성 확보를 위해 측정 데이터 처리 표준프로토콜 개발, XML 또는 PDF-A3 형태 등의 DCC 표준 포맷 및 기계가독형(machine readable) DCC 형식 개발 등을 진행하고, 자동생성 DCC의 신뢰성을 확보할 수 있는 국가측 정표준 디지털 기준점 구현 기술, AI 기반 DCC 오류 판독기술 등을 개발
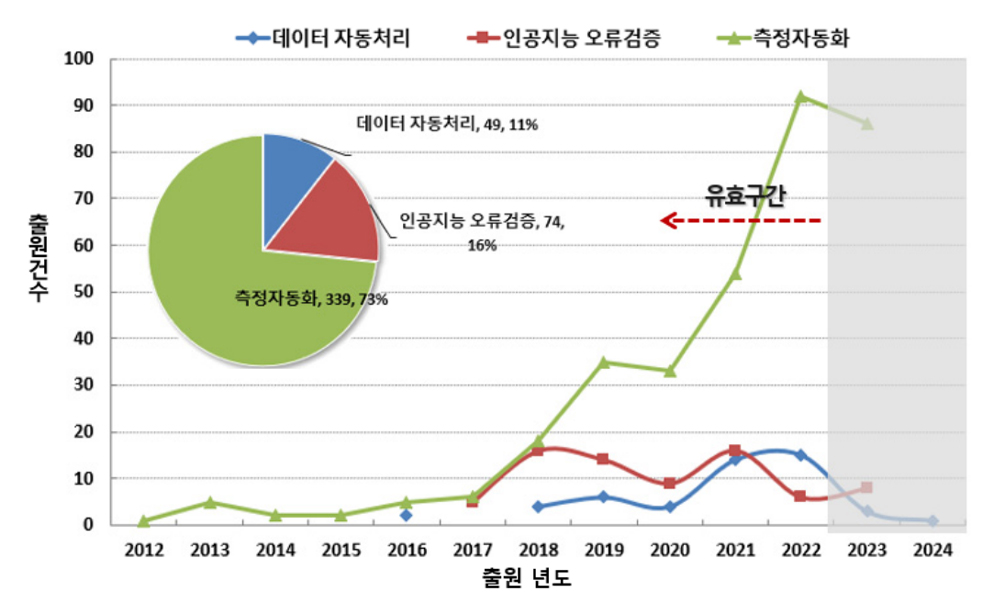
<자료> 한국표준과학연구원 자체 작성
[그림 4] 측정기술 디지털화 관련 특허 동향
③ (디지털 보급체계 현장 활용성 극대화를 위한 DCC 적용 실증기술) DCC 기술을 통해 국가측정표준 보급체계를 디지털화하기 위해서는 국가인증제도 아래의 교정 기관이 현장에서 적용해야 하므로[그림 4], 국가 소급체계 DCC 임베딩 기술, 현장 교정시험장비 DCC 자동 적용기술, 현장 교정시험장비 DCC 적용 실증 기술 등을 개발
특허 분석을 통해 관련 산업계의 동향을 간략하게 살펴보면 AI, 빅데이터, 기계학습과 같은 디지털 기술의 급속한 발전과 함께 출현한 4차 산업혁명의 진전에 힘입어 측정 기술 디지털화 관련 특허는 2018년 이후 급격하게 출원이 증가하였으며, 출원국가 및 출원인의 국적으로 분류하면 각각 미국이 50% 정도의 점유율로 관련 산업 동향이 가장 활발하다.
III. 디지털화를 위한 측정기술
측정표준이 디지털화되어 산업현장과 직결되면 엄청나게 많은 소자 단위의 센서에서 부터 생산설비 전체에 해당하는 대규모 시스템 레벨까지의 다양하고 많은 측정과 교정을 주기적으로 수행하고 관리해야 할 것이다. 센서의 다양성에 대응하기 위해 길이, 질량, 방사선, 가속도, 전기, 전자파 등 다양한 물리량의 측정 정밀도는 확보하였지만, 대량의 센서를 평가하기 위한 대응 체계와 시스템 레벨의 연동을 통한 현장 측정기술 등은 지속 적으로 연구되어야 할 과제이며 이와 연관된 기술을 소개한다.
1. 지능형 로봇을 이용한 측정자동화 기술 작업자의 단순하고 반복적인 전처리 과정이 필요하거나 위험에 노출될 수 있는 센서 평가에는 지능형 로봇을 적용하여 생산성을 높일 수 있다. [그림 5]의 왼쪽은 일본에서 활용되고 있는 인증표준물질의 전처리 dual arm robotic platform이며[6], 오른쪽은 미국 NIST에서 운용되고 있는 로봇을 이용한 안테나 측정시스템이다[7]. 지능형 시스템이 되기 위해서는 거리, 위치, 패턴 인식을 통한 정렬 및 위치 제어가 가능해야 하므로 비전, 초음파, 라이다 등 센서의 결합이 필요하다. 단순 반복 측정에서의 휴면 에러 방지, 산업 인력의 부족 등을 고려할 때 지능형 로봇을 이용한 측정 자동화는 필수적이다.
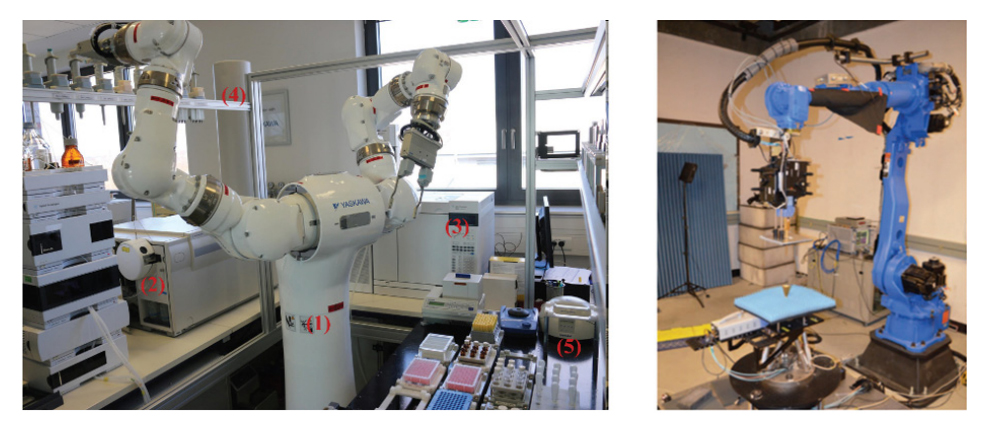
<자료> N. Yachie, Robotic Biology Consortium, and T. Natsume, “Robotic crowd biology with Maholo LabDroids,” Nature Biotechnology, Vol. 35, Num. 4, 310-312, Apr. 2017.
J. A. Gordon, D. Novotny, and M. Allman, “Precision optical antenna alignment system for tracking antennas in 6-DOF,” AMTA, Williamsburg, Nov. 2018.
[그림 5] 로봇을 이용한 측정 자동화
2. 현장형 측정시스템 측정을 통한 디지털화된 성능 검증 데이터는 제품의 생산 단계에서도 중요하지만 4차 산업 환경 내에 적용된 이후의 성능 유지 검증을 위해서도 활용된다. 이때 센서 또는 장비 단위의 성능 검증을 위해 생산 프로세스를 장시간 멈추고 대상물을 분리하여 성능 검증 환경으로 이동하면 생산성과 비용면에서 큰 손실이 될 수 있다. 이와 같은 손실을 최소화하기 위해 측정 대상물이 위치한 곳으로 이동하여 성능 검증을 수행하는 현장형 (on-site) 측정시스템이 제안되고 있다. [그림 6]은 NASA(National Aeronautics and Space Administration)에서 개발된 현장형 통신 모듈 OTA(Over The Air) 평가 시스 템으로 실험비행체, 드론 등에 탑재된 통신 모듈을 비행체와 분리하지 않고 측정시스템이 격납고로 이동하여 평가를 수행한다[8]. 현장에서의 측정 데이터의 정밀도를 높이기 위해 레이저를 이용한 위치 정보 획득과 협동로봇을 이용한 측정 수행 등 다양한 첨단 기술과 함께 구현된다. 향후 스마트팩토리, UAM(Urban Air Mobility), 자율주행차량 등이 보급 확대되면 현장형 측정시스템의 수요는 지속적으로 늘어날 것으로 예상된다.
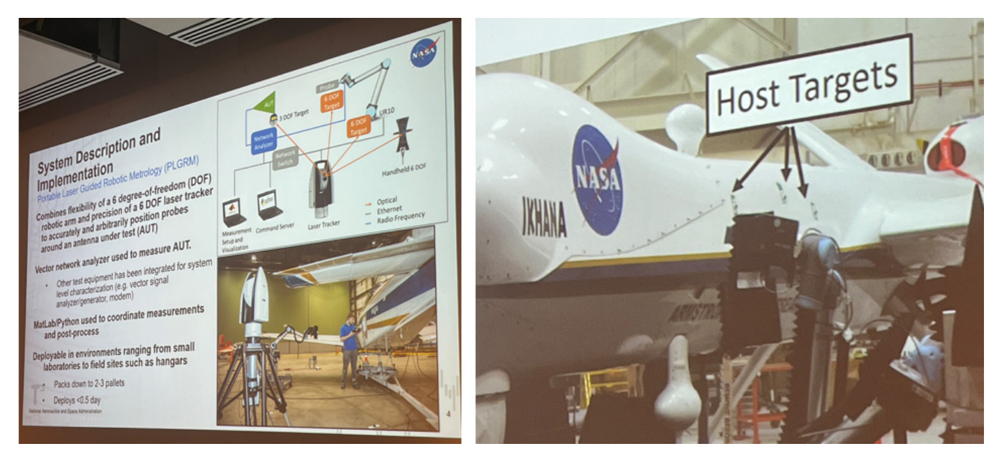
<자료>한국표준과학연구원 자체 작성
[그림 6] 현장형 측정시스템을 이용한 통신 모듈의 OTA 측정
최근 국내에서도 로봇 기반 현장형 측정시스템이 개발 중이며 전자파 센서에 해당하는 표준 안테나의 평가는 상당 부분 자동화가 되었으며, 특히 차세대통신의 핵심부품이 될 위상배열안테나와 RIS(Reconfigurable Intelligent Surface) 측정과 평가를 위한 기술 개발은 계속 진행되고 있다[그림 7][9].
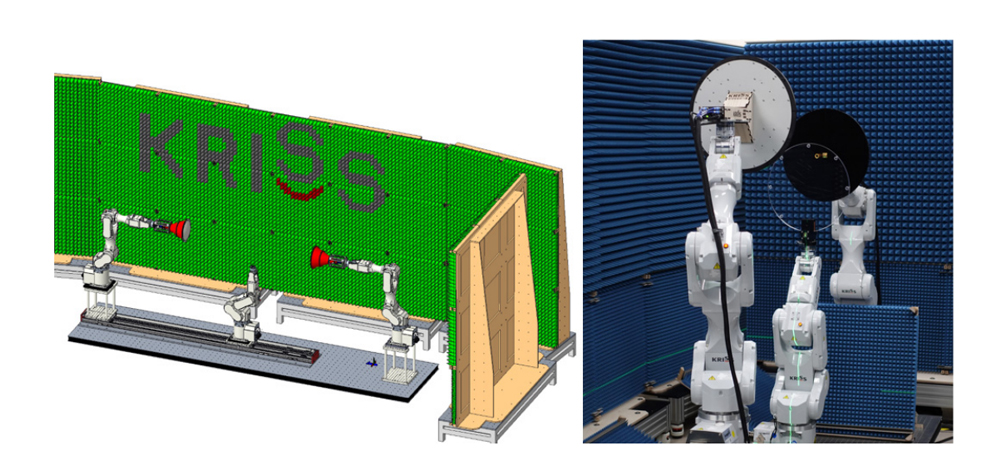
<자료> 한국표준과학연구원 자체 작성
[그림 7] 로봇 기반 전자파측정 시스템
위상배열안테나는 수백~수천 개 단위의 안테나 모듈의 조합이므로 개발 단계의 평가 에서는 모듈 단위의 위치 정보를 포함한 모듈별, 주파수별 전자파 방사 특성 등 매우 많은 특성 데이터가 요구되어 매우 긴 시간의 측정/평가/조정의 과정을 거친다. 특성 데이터가 디지털화되어 손쉽게 주고받을 수 있게 된다면 위상배열안테나의 조정 과정이 획기적으로 짧아질 것이다.
커버리지 확장 기술로 주목받는 RIS의 측정과 평가 기술은 현장형 측정이 가능해야 할 것으로 예측되며 커버리지 확장성을 계량화할 수 있는 측정 기술이 필요할 것이다.
Ⅳ. 결론
기술과 산업이 발전함에 따라 의사결정 단계에서 측정표준을 기반으로 하는 다양하고 정확한 측정 데이터의 충분한 확보와 가치사슬 내의 빠르고 정확한 측정 데이터 전달의 중요성은 계속 높아지고 있다. 이에 따라 측정표준 역시 전통적인 체계에서 벗어나 능동 적으로 측정 정확도를 높이고 관리 자동화를 지향하는 전달 체계로 전환이 필요하다.
주요 선진국에서는 지능형 로봇을 이용한 측정 자동화 기술과 현장형 측정시스템 등을 개발하여 측정 데이터의 대량 생산과 원활한 공유를 위해 측정표준의 디지털화 연구를 지속하고 있다. 우리나라도 측정표준과 측정 기술이 4차 산업체계에 적극적으로 활용될 수 있도록 연구개발, 제도 마련 등 다양한 노력이 필요하다.
[1] Frost & Sullivan, “Industry 4.0, the Fourth Revolution: Challenges, Benefits, Adoption and How to Begin”, A Frost & Sullivan White Paper, 2019.
[2] SAP, “The Digital Transformation of Manufacturing Companies SAP’s Strategy for Industry 4.0”, SAP White Paper, 2021.
[3] 대한민국 국가표준기본법, 법률 제15643호, 2018.
[4] R. Hanisch et al., “Stop squandering data: make units of measurement machine-readable”, Nature, 605, 222-224, 2022.
[5] KRISS, 신규 기본사업 기획보고서, 국가측정표준 보급체계 디지털화 통합플랫폼 개발 및 실증, 2024. [6] N. Yachie, Robotic Biology Consortium and T. Natsume, “Robotic crowd biology with Maholo LabDroids”, Nature Biotechnology, Vol. 35, Num. 4, 310-312, Apr. 2017.
[7] J. A. Gordon, D. Novotny and M. Allman, “Precision optical antenna alignment system for tracking antennas in 6-DOF”, AMTA, Williamsburg, Nov. 2018.
[8] M. Piasecki, B. Schoenholz, J. Downey and K. Lambert, “Robotic arm-based antenna metrology system for aerospace applications”, EuCAP, Glasgow, March 2024.
[9] J.-Y. Kwon, W. Jung and C. Cho, “KRISS Robot-based antenna measurement system”, EuCAP, Glasgow, March 2024.